- Zdroj:
- Unsplash
- Autor:
- Ant Rozetsky
- Licence:
- Unsplash License
Jak dekarbonizovat výrobu oceli?
Obsah
Výroba oceli je emisně velmi náročná. Zároveň se jedná o materiál, který je pro fungování moderní společnosti naprosto zásadní. Proto je dekarbonizace tohoto průmyslového sektoru velice důležitá. Cest k ní vede několik a každá má své výhody i nevýhody.
Ocel je jednou z nejdůležitějších surovin a lidstvo ji využívá ve stavebnictví, dopravě, průmyslu i mnoha dalších odvětvích. V technické praxi se rozlišují různé druhy ocelí a litin, někdy se také odděluje výroba surového železa a jeho další zpracování. Pro základní představu o možnostech dekarbonizace ale nejsou tyto detaily příliš podstatné, a proto se jimi tento text nezabývá.
Výroba oceli a emise skleníkových plynů
Jak se na dekarbonizaci dívají v jedné z oceláren v Česku
Rozhovor s oceláři přináší tato epizoda podcastu 2050.
Celkově se na světě ročně vyrobí 1,9 miliard tun oceli.1 Většina této produkce (okolo 75 %) probíhá ve vysokých pecích, kde se spaluje uhlí či koks. Zbývajících 25 % připadá na elektrické obloukové pece, případně na tzv. přímou redukci železa. Tyto dva výrobní postupy se velmi liší svou emisní intenzitou.2 Zatímco v případě surového železa vyráběného ve vysokých pecích připadá na každou vyrobenou tunu oceli cca 2,3 tuny oxidu uhličitého (t CO2), při recyklaci železa v pecích obloukových vzniká na 1 tunu oceli pouze 0,6 t CO2. Celosvětově je průměrná emisní intenzita výroby oceli 1,9 t CO2 na tunu oceli,3 v jednotlivých zemích však může být toto číslo velmi různé – vždy záleží na konkrétním poměru výrobních technologií.4
Celkově představuje výroba oceli 7 % světových emisí skleníkových plynů a 11 % světových emisí CO2. Zhruba polovina těchto emisí vzniká při spalování uhlí (koksu), druhá polovina při chemické reakci.5 Železné rudy jsou totiž sloučeniny železa s kyslíkem (například Fe3O4, Fe2O3)6 a při výrobě surového železa je nutné tento kyslík z rudy vyvázat (tzv. redukční reakce). K tomu se ve vysokých pecích používá koks, který slouží nejen jako palivo, ale i jako redukční činidlo (uhlík z koksu na sebe naváže kyslík z rudy).
Protože uhlí (koks) je fosilní palivo, jedna z klíčových cest pro dekarbonizaci výroby surového železa spočívá v tom použít namísto uhlíku vodík – při redukční reakci pak nevzniká CO2, ale voda. Technologicky však jde o jiný proces a vodík není možné používat v současných vysokých pecích.
Dekarbonizace výroby oceli
Tento průmyslový sektor bude obtížné dekarbonizovat (patří k tzv. hard-to-abate sectors). Existují už ale první projekty, které ukazují, že nízkoemisní ocel vyrábět lze.
Je tedy na místě zvažovat, jak lze tyto projekty škálovat, kolik to bude stát a jak se to projeví na celkových emisích z výroby oceli. Na tyto a další otázky se snaží odpovědět tzv. sektorové dekarbonizační scénáře, což jsou studie možného vývoje sektoru výroby oceli, který by vedl k nízkým nebo nulovým emisím skleníkových plynů.
V dalším textu vycházíme z dekarbonizačních scénářů těchto institucí:
- IPCC: Sixth Assessment Report – Working Group III: Kapitola 11
- Mission Possible Partnership: Making Net Zero Steel Possible
- Mezinárodní agentura pro energii: Iron and Steel Technology Roadmap
- McKinsey: Transition to Net Zero: Steel
- World Economic Forum: Net Zero Industry Tracker (2022)
Všechny tyto scénáře se shodují v několika obecných rysech:
- Výroba oceli v budoucnu mírně poroste a lze očekávat, že v roce 2050 bude o 10–40 % vyšší než dnes. Při využívání současných technologií by to znamenalo nárůst emisí z dnešních cca 3 Gt CO2 na 4–4,5 Gt CO2.
- Scénáře zpravidla nepočítají s úplnou dekarbonizací sektoru. Například scénář Making Net Zero Possible směřuje k emisím okolo 0,3 Gt CO2 v roce 2050. To je nicméně už jen malá část současných emisí v tomto odvětví.
- Dominantní roli v dekarbonizaci hrají tři technologie: využití zeleného či nízkoemisního vodíku, CCS a recyklace, přičemž každá z těchto technologii by se mohla na snížení emisí podílet 20–30 %. Podrobnosti o těchto technologiích a možnostech jejich nasazení jsou uvedeny níže. Míra jejich využití totiž bude záviset na situaci v daném regionu.
- Dekarbonizovaná ocel bude dražší, u zelené oceli se očekává zvýšení ceny o 25–50 %. Na cenách koncových výrobků se ale toto zvýšení ceny oceli projeví jen málo. Automobil či dům, v nichž je použita nízkoemisní ocel, bude stát cca o 1 % více než ten, který využívá ocel vyrobenou současnými technologiemi7 – cena oceli tvoří zpravidla pouze zlomek celkové ceny produktu.
- Zpoplatňování emisí skleníkových plynů (např. systém EU ETS) bude zvyšovat konkurenceschopnost nízkoemisní oceli. Lze očekávat, že při cenách 180–360 dolarů za tunu CO2 by byla nízkoemisní ocel stejně drahá jako ocel vyráběná současnými metodami (nebo i levnější). Podobně se například ceny přiblíží nebo zcela srovnají v důsledku Inflation Reduction Act (IRA) v USA, který poskytuje významné slevy na daních podnikům, které vyrábějí zelený vodík a zachytávají CO2.8
Jaké technologie je možné využít?
Přímá redukce železa zeleným vodíkem
Umožňuje nahradit emisně nejnáročnější část výroby oceli – vysoké pece, ve kterých se jako palivo i jako redukční činidlo používá koks. Takto vyrobené surové železo je pak nutné dále zpracovávat v elektrických obloukových pecích. Nutnou podmínkou je dostupnost vodíkové infrastruktury (elektrolyzéry, skladovací kapacity nebo produktovody). Cena zeleného vodíku, a tedy i cena oceli vyráběné s jeho využitím, pak bude závislá na ceně elektřiny – a lze proto očekávat, že tento způsob bude využíván zejména v oblastech s dostatkem obnovitelných zdrojů. Kromě toho by přechod na výrobu oceli pomocí zeleného vodíku vyžadoval velké investice do nových typů vysokých pecí. V důsledku zmíněných faktorů se tak redukce zeleným vodíkem uplatní jen asi u třetiny očekávané výroby oceli, přestože vypadá jako nejvíce přímočaré řešení.
Zachytávání CO2 (CCS)
Na vysoké pece je možné nainstalovat zařízení na zachytávání oxidu uhličitého (tzv. CCS). Tato zařízení dokáží zachytit 90–95 % emisí CO2 dané ocelárny. Čím je ovšem míra zachytávání vyšší, tím je proces také energeticky a finančně náročnější. Technologie zachytávání CO2 je zatím ve fázi drobných pilotních projektů.9 Nutnou podmínkou pro větší využití CCS je dostupnost geologických úložišť pro zachycené CO2.
Recyklace a čistá elektřina
Při současné recyklaci oceli v elektrických obloukových pecích vzniká ve srovnání s výrobou ze surového železa ve vysokých pecích jen zlomek emisí (při běžném mixu elektřiny je to 0,6 tuny CO2 na tunu oceli oproti 2,3 tuny CO2 při výrobě ve vysoké peci). Pokud by byly obloukové pece napájeny z nízkoemisních zdrojů elektřiny (obnovitelné zdroje nebo jádro), vyráběly by prakticky bezemisní ocel. Již dnes jde o používanou technologii, například v USA se takto vyrábí 70 % oceli.8 Celkově se na světě recykluje okolo 85 % oceli,10 klíčovým limitem pro využití této technologie bude dostupnost železného šrotu (ocel je materiál s dlouhou životností, objem využitelného šrotu je tedy relativně omezený).
Doplňkové a nové technologie
Mezi doplňkové metody patří například přímá redukce železa pomocí zemního plynu, která je vhodná v regionech, kde je plyn levný a dostupný (například v USA či Rusku). Emisní intenzita v tomto případě dosahuje 1 tuny CO2 na tunu vyrobené oceli, oproti výrobě ve vysokých pecích je tedy emisní stopa více než o polovinu nižší.8 Dále je částečně možné jako palivo či redukční činidlo využívat biomasu. Vzhledem k potřebě velkého množství biomasy bude nicméně tato metoda nejspíš využívána jen omezeně, v regionech s vysokou dostupností biomasy, jako je Brazílie či Rusko.11 Využití biomasy ovšem s sebou nese i environmentální rizika a šetrnost řešení je často sporná. Dalšího drobného snížení emisí lze dosáhnout například zvyšováním efektivity existujících pecí či využíváním železných rud s vyšším obsahem železa.
Nově zkoumanou technologií je elektrolýza železné rudy v roztaveném, příp. rozpuštěném stavu (molten oxide electrolysis, MOE). Výhodou je přímá výroba oceli z železné rudy bez mezistupně surového železa. Technologii lze použít pro výrobu vysoce čistého železa i jiných kovů. Technologie rovněž nezávisí na výrobě a ukládání vodíku. Technologie má dva podtypy: vysokoteplotní MOE (1500–1600 °C) a nízkoteplotní MOE (pod 150 °C). Oba procesy využívají stejnosměrný proud, který produkují například fotovoltaické panely a většina chemických baterií. Vysokoteplotní MOE musí navíc udržovat vysokou teplotu po dobu mnoha hodin, což může být náročné zajistit z nízkoemisních zdrojů. Tato technologie se nachází ve vývojové fázi a je málo pravděpodobně, že by měla komerční využití v nejbližším desetiletí. V případě, že by se podařilo dosáhnout škálování a výrazného zlevnění, může se MOE stát jednou z hlavních metod dekarbonizace výroby oceli. Dnes se ovšem stále jedná o experimentální metodu.
Co ovlivní průběh dekarbonizace?
Budoucnost konkrétní ocelárny bude záležet na řadě faktorů: na výši státní podpory pro tyto podniky, vzdálenosti od geologického úložiště pro zachycené CO2 či na ceně zeleného vodíku a navazující infrastruktuře. V případě neúspěšné transformace se může stát, že některé ocelárny zaniknou, protože se výroba přesune někam, kde bude levný vodík či CCS. Zdroje často ovlivňovaly umístění ocelárny i v minulosti (například blízkost uhelných dolů).
Zároveň státy pokládají výrobu oceli za strategické průmyslové odvětví. Proto i když transformace probíhá v tržním prostředí, kde spolu různé ocelárny soutěží cenou, budou vlády výrobu nebo její dekarbonizaci významně podporovat. Do určité míry se to děje už dnes a přímé i nepřímé formy státní podpory může do budoucna ještě přibývat.
Hlavní opatření, které budou průběh dekarbonizace sektoru ovlivňovat:
- Mechanismy snižující rozdíly v cenách nízkoemisní a vysokoemisní oceli: ceny emisních povolenek či uhlíkové daně, investiční podpora (v EU například prostřednictvím Inovačního fondu), daňové úlevy na zavádění potřebných technologií (v USA například daňové úlevy na výrobu zeleného vodíku) nebo tzv. systém uhlíkového vyrovnávání na hranicích (CBAM).12
- Poptávka po nízkoemisní oceli: zpracovatelé mohou o nízkoemisní oceli uvažovat i v případě, že bude dražší – protože se například zavázali snižovat svou uhlíkovou stopu nebo po nich výrobky s nižší emisní stopou budou chtít koncoví zákazníci.
- Rozvoj výroby zeleného vodíku a technologií pro zachytávání CO2.
V následujících letech bude stát mnoho oceláren před rozhodnutím, kterou cestou dekarbonizace se vydat. Tato rozhodnutí zásadně ovlivní jejich dlouhodobé fungování, na druhou stranu se musí rozhodovat v prostředí plném nejistot – například plán na využití zeleného vodíku se může ukázat jako nevhodný, jestliže bude rozvoj jeho výroby pomalý nebo cena vysoká. Tato nepřehlednost prostředí vede k tomu, že mnoho výrobců oceli s potřebnými investicemi zatím vyčkává.
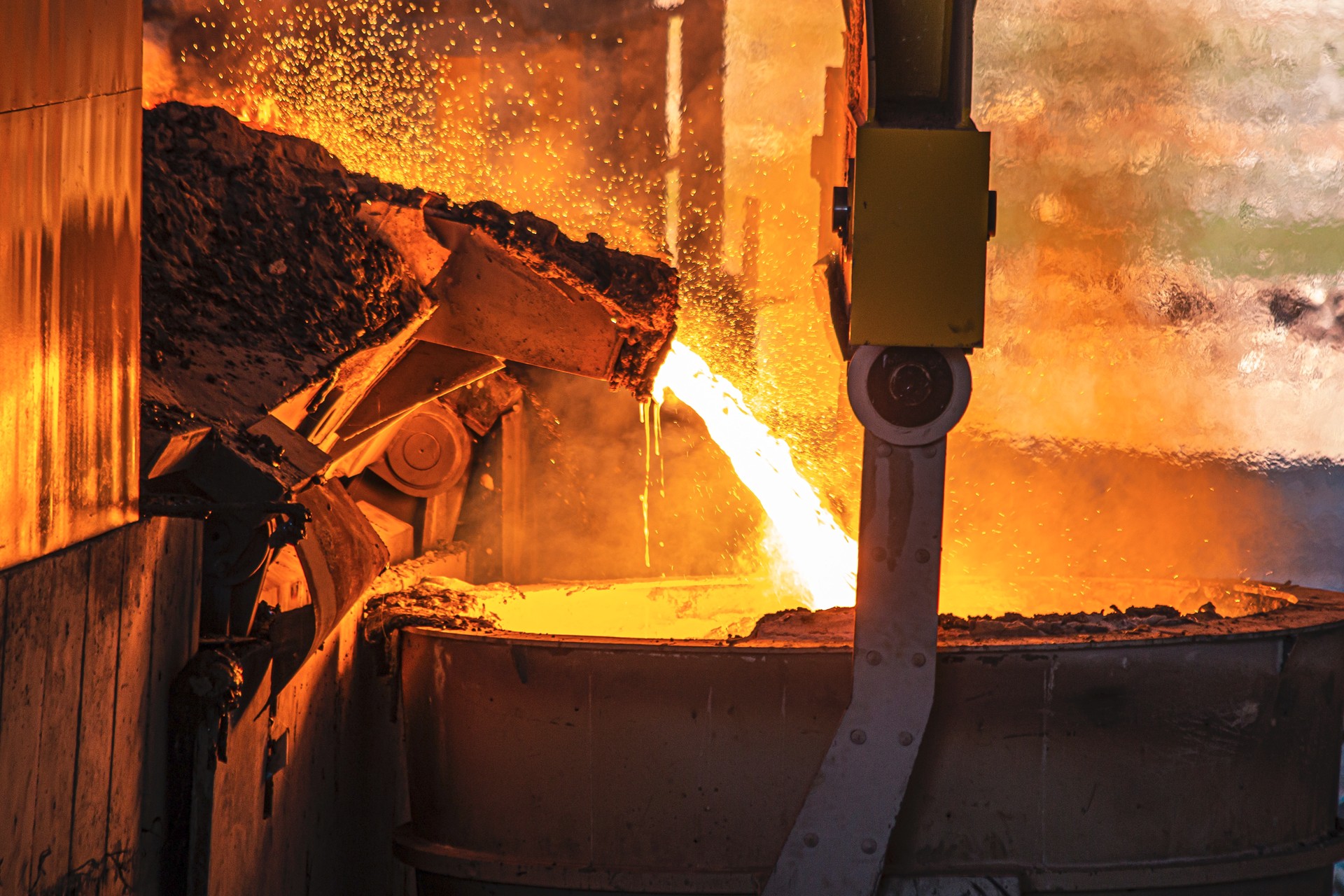
1 tuna oceli = cca 1,9 tun CO2
Poznámky a zdroje
-
Zatímco Světové ekonomické fórum WEF: Net Zero Industry Tracker (2022) uvádí průměrnou světovou emisní intenzitu výroby oceli 1,9 t CO2, Mezinárodní agentura pro energii (IEA) uvádí průměrnou světovou emisní intenzitu 1,4 t CO2 na tunu vyrobené oceli. Rozdíl mezi těmito údaji o emisní intenzitě je pravděpodobně způsoben různým započítáváním nepřímých emisí (scope 2), případně může souviset s tím, které procesy jsou do výroby oceli započítávány. ↩︎
-
Studie Steel Climate Impact uvádí emisní intenzity pro řadu zemí. Zatímco například v USA je průměrná emisní intenzita přibližně 1 t CO2 na tunu vyrobené oceli, v Německu je to 1,5 t CO2 a v Číně okolo 2 t CO2. Hlavní rozdíl spočívá v rozdílném poměru mezi výrobou ve vysokých pecích (tedy výrobou surového železa) a výrobou v obloukových pecích (tedy recyklací oceli) v jednotlivých zemích. ↩︎
-
World Economic Forum, 2022: Net Zero Industry Tracker 2022 Edition. ↩︎
-
Boston Consulting Group: Impact of IRA, IIJA, CHIPS, and Energy Act of 2020 on Clean Technologies. V USA stojí tuna oceli vyrobená konvenční cestou ve vysoké peci 360 dolarů. Díky podpoře zeleného vodíku v rámci IRA může tuna surové oceli vyrobené pomocí zeleného vodíku stát 370 dolarů. ↩︎ ↩︎2 ↩︎3
-
MIT, 2021: How efficient is carbon capture and storage?. Očekávaná cena zachytávání CO2 se podle IEA pohybuje kolem 35–95 eur (900–2 250 Kč) za tunu CO2. Cena oceli závisí na druhu požadovaného produktu a místě výroby, v západní Evropě se průměrná cena podle Steel Benchmarker pohybuje kolem 700–800 eur (16 700–19 100 Kč). ↩︎
-
Yale Environment 360, 2021: Can the World’s Most Polluting Heavy Industries Decarbonize? ↩︎
-
McKinsey&Company, 2020: Decarbonization challenge for steel ↩︎
-
Evropská komise: Mechanismus uhlíkového vyrovnání na hranicích: Otázky a odpovědi ↩︎
Související infografiky a studie
Zaujala vás naše práce? Prozkoumejte další související infografiky a studie: